The Stages Of Porcelain And China Restoration
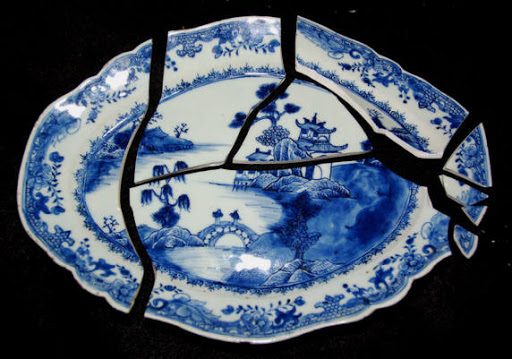
After a detailed condition report, porcelain restoration protocol is proposed. Several parameters are taken into account: the fragility of the ceramic, the visibility of the restoration, the legibility of the object, its value can also be considered.
Cleaning
The first fundamental step is cleaning, i.e., eliminating dust, traces of grease, old aged restorations, and yellowed glues, which no longer fulfill their role of adhesive correctly and put the object in danger. But cleaning does not mean stripping, we clean as much as possible respecting the patina and the traces of time gone by which give the object the charm of the old.
Collage
Once the object has been cleaned, the actual restoration can begin. Before any bonding, you must know the nature of the ceramic paste that you are treating because not all of them will benefit from the same restoration protocol. We always use an adhesive less concrete than ceramic paste to avoid any stress on the material.
A friable African terracotta fired at low temperature (400 ° C) will be glued with vinyl or acrylic glue to adapt to its high porosity. Conversely, a porcelain with almost zero porosity thanks to the silica it contains will be bonded with an epoxy adhesive, the crosslinking of which becomes three-dimensional during drying.
Filling
Like adhesives, there are different filling materials used depending on the nature of the ceramic: dental plaster, stucco enriched or not with vinyl glue for more resistance, polyester mastic, epoxy mastic and all can be tinted in the mass to using mineral pigments or dyes to match the color of the paste or the enamel.
Any lost shapes can be reproduced by casting or by documented creation.
As a general rule, we will always choose a filling material that is less solid than the ceramic itself to avoid damaging it during sanding.
Retouching
As with all the restoration products mentioned up to now, there are several types of paint depending on the ceramic to be treated and the degree of restoration chosen. As part of a careful restoration, the patterns can be restored with a brush to give the illusion of continuity; acrylic and polyurethane resin can be used as well.
For retouching terracotta, we will use acrylic paint applied with a sponge to restore the velvety appearance of the material. While the invisible restoration of porcelain requires the essential use of polyurethane paints applied with an airbrush.
The precision of the airbrush is such that it allows us not to perform an invasive restoration and to confine ourselves to the gap to respect the authenticity of the object.
Once the background color is applied with an airbrush, it is protected by a transparent varnish. The patterns can then be reproduced and applied with a brush: flat, blurred, raised patterns … the whole is covered with one or more thin layers of varnish all sanded between each application.
Depending on the case, the last layer of varnish can be sanded and polished with polishing paste.
Gilding
As during the manufacture of the object, the gilding is applied last, it’s firing temperature being much lower than the other colors. The gilding is carried out by applying gold leaves of different carats depending on the shade to be reproduced or by mixing gold powder and polyurethane resin for the most delicate patterns.